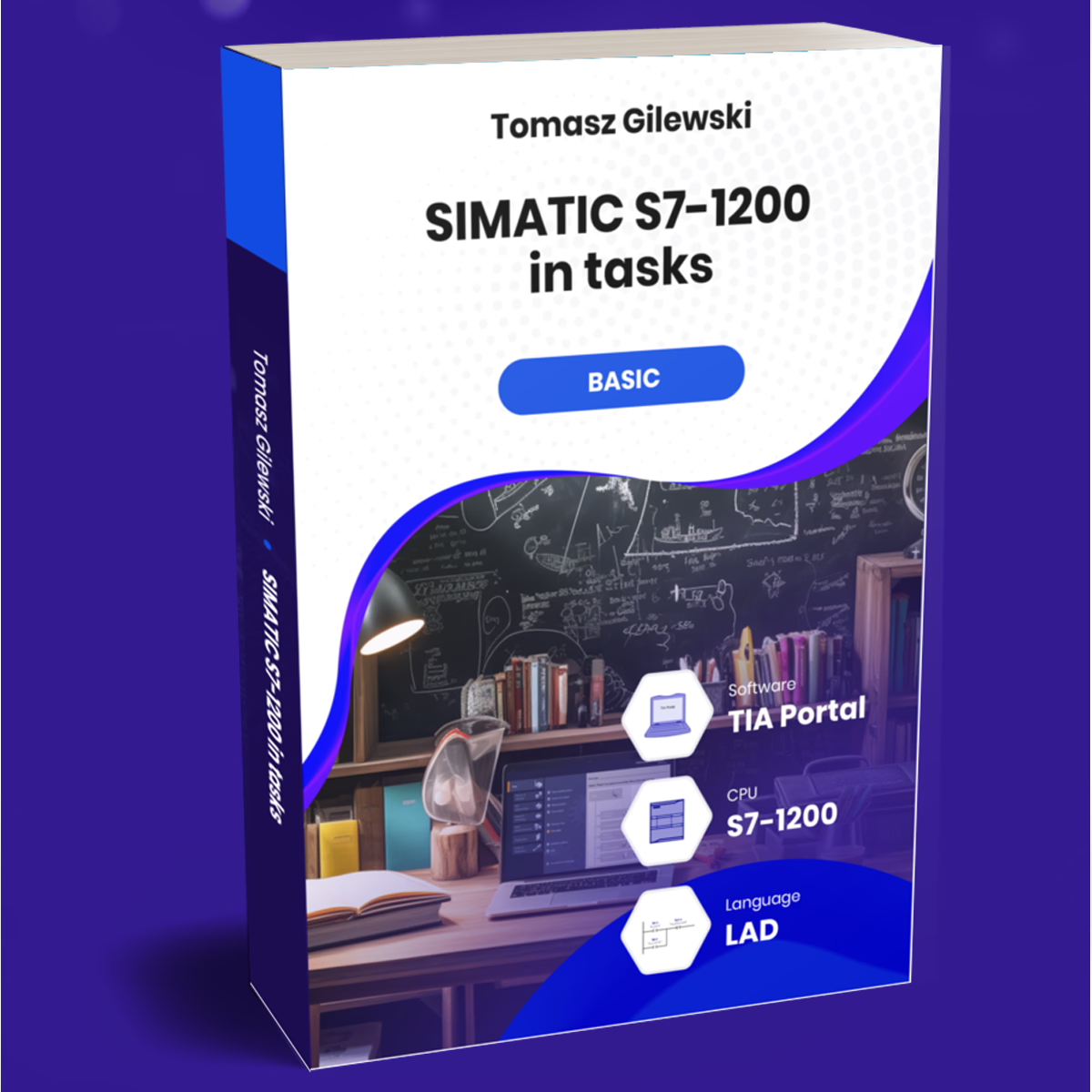
SIMATIC S7-1200 in tasks. LAD language. Basic level
Book details:
Author: Tomasz Gilewski
Publisher: PLCspace
Pages: 149
Print: –
Format: e-book
Invoice: Yes
VAT PROFORMA: Yes
Condition: New
39.00 PLN
Introduction to Programming in Modern Times
Nowadays, programming skills are becoming more and more desirable on the labor market. Regardless of the industry, programming has become an integral element of many business and technological processes.
Learning Programming: Materials and Tools
There are many resources and tools to help you develop your programming skills, such as books, online courses, mobile apps, and much more. The choice depends on your preferences and level of advancement.
Developing Skills Through Practice
Developing Skills Through PracticeOne of the best ways to develop programming skills is to learn through practice. Creating projects and solving programming problems allows you to gain practical experience.
The book "Simatic S7-1200 in Tasks. LAD Language. Basic level"
If you want to learn programming in the LAD language, our book "Simatic S7-1200 in Tasks. LAD Language. Basic level" is the key to achieving this goal. The book offers practical exercises and examples, helping you to gradually master the LAD language.
Benefits of Mastering the LAD Programming Language
Mastering the LAD programming language will allow you to create unique projects in various industrial fields, such as automation, robotics, energy and processing.
The Importance of Task Solutions
A book with solutions to tasks is a valuable tool for developing programming skills. It helps you understand theory in practice, saves time and avoids mistakes.
Development of Creativity and Independence
The book allows you to develop creativity, independence in problem solving and gain confidence in programming through a variety of task scenarios.
Summary
A book with solutions to tasks allows you to master programming skills faster through the practical use of theory in specific tasks. Access to proven solutions increases the efficiency of the programming process, enabling the creation of advanced systems that meet the needs of modern PLC applications.
Table of contents:
1 Preparation – what you will need. 7
2 Description of the facility. 7
3 From process to PLC programming.. 10
4 Bitwise operations. 11
4.1 Task 3a – Driving to the sensor (NC type) – AND gate.. 11
4.1.1 Resolution. 11
4.1.2 Scenario 1. 11
4.1.3 Scenario 2. 12
4.1.4 Scenario 3. 12
4.1.5 Scenario 4. 13
4.2 Task 3b – Driving to the sensor (NO type) – AND gate.. 13
4.2.1 Solution. 14
4.2.2 Scenario 1. 14
4.2.3 Scenario 2. 14
4.2.4 Scenario 3. 15
4.2.5 Scenario 4. 16
4.3 Task 3c – Conveyor driving – OR gate.. 17
4.3.1 Resolution. 17
4.3.2 Scenario 1. 17
4.3.3 Scenario 2. 18
4.3.4 Scenario 3. 19
4.3.5 Scenario 4. 20
4.4 Task 3e – Conveyor driving – OR and AND gate.. 20
4.4.1 Solution. 20
4.4.2 Scenario 1. 21
4.4.3 Scenario 2. 21
4.4.4 Scenario 3. 21
4.4.5 Scenario 4. 22
4.4.6 Scenario 5. 22
4.5 Task 3f - Conveyor driving (shutdown dominance). 22
4.5.1 Resolution. 23
4.5.2 Scenario 1. 23
4.5.3 Scenario 2. 23
4.5.4 Scenario 3. 24
4.5.5 Scenario 4. 24
4.5.6 Scenario 5. 25
4.6 Task 3g - Conveyor driving (on dominance). 25
4.6.1 Resolution. 25
4.6.2 Scenario 1. 26
4.6.3 Scenario 2. 26
4.6.4 Scenario 3. 26
4.6.5 Scenario 4. 27
4.6.6 Scenario 5. 27
5 Flip-flops 29 29
5.1 Task 4g - Moving the conveyor from sensor to sensor (switch-off dominance). 29
5.1.1 Resolution. 29
5.1.2 Scenario 1. 29
5.1.3 Scenario 2.30
5.1.4 Scenario 3. 31
5.1.5 Scenario 4. 31
5.1.6 Scenario 5. 32
5.1.7 Scenario 6. 33
5.1.8 Scenario 7. 33
5.1.9 Scenario 8. 34
6 M memory (markers). 35. 35
6.1 Task 5a_0 - Moving the conveyor from sensor to sensor (switch-off dominance). 35
6.1.1 Resolution. 36
6.1.2 Scenario 1. 37
6.1.3 Scenario 2. 38
6.2 Task 5a_1 - Moving the conveyor from sensor to sensor (switch-off dominance). 39
6.2.1 Resolution. 40
6.2.2 Scenario 1. 41
6.2.3 Scenario 2. 42
6.2.4 Scenario 3. 43
6.2.5 Scenario 4. 44
6.2.6 Scenario 5. 46
6.3 Task 5c_1. 47
6.3.1 Resolution. 47
6.3.2 Scenario 1 – Heading left. 48
6.3.3 Scenario 2 - Left direction. 50
6.3.4 Scenario 3 - Heading left. 52
6.3.5 Scenario 4 - Heading left. 53
6.3.6 Scenario 5 - Heading left. 54
6.3.7 Scenario 6 - Heading left. 57
6.3.8 Scenario 1 - Right direction. 59
6.3.9 Scenario 2 - Right direction. 60
6.3.10 Scenario 3 - Direction to the right. 61
6.3.11 Scenario 4 - Direction to the right. 64
6.4 Task 5c_2. 65
6.4.1 Resolution. 65
6.4.2 Scenario 1. 66
6.4.3 Scenario 2. 67
6.4.4 Scenario 3. 69
6.4.5 Scenario 4. 71
6.4.6 Scenario 5. 72
6.4.7 Scenario 6. 74
6.4.8 Scenario 7. 76
7 System memory. 78 78
7.1 Task 6a – System byte 78
7.1.1 Termination. 78
7.1.2 Scenario 1. 78
7.1.3 Scenario 2. 79
8 Slopes. 81 81
8.1 Task 8a - Stopping product transport after passing the sensor. 81
8.1.1 Termination. 81
8.1.2 Scenario 1. 82
8.1.3 Scenario 2. 83
8.2 Task 8b - Start/Stop transport with the di_Start button 84 di_Start 84
8.2.1 Resolution. 85
8.2.2 Scenario 1. 86
8.2.3 Scenario 2. 87
8.2.4 Scenario 3. 89
9 Jumps 91 91
9.1 Task 9a - Turning the green LED light on/off. 91
9.1.1 Termination. 92
9.1.2 Scenario 1. 92
9.1.3 Scenario 2. 93
9.1.4 Scenario 3. 94
9.1.5 Scenario 4. 96
10 MOVE Statement.. 97. 97
10.1 Task 12 - Writing a value to a variable (memory area M). 97
10.1.1 Termination. 97
10.1.2 Scenario 1. 97
10.1.3 Scenario 2. 98
11 Conversion. 99 99
11.1 Task 17 - Converting the value from the BCD..99 setpoint
11.1.1 Termination. 99
11.1.2 Scenario 1.99
11.1.3 Scenario 2. 100
11.1.4 Scenario 3. 101
11.1.5 Scenario 4. 102
12 Arithmetic calculations. 103 103
12.1 Task 18 - increment. 103
12.1.1 Termination. 103
12.1.2 Scenario 1. 104
12.1.3 Scenario 2. 106
12.2 Math Problem 18 - Calculating the belt speed in mm/s. 107
12.2.1 Termination. 107
12.2.2 Scenario 1. 109
12.2.3 Scenario 2. 111
13 CALCULATE statement. 113 113
13.1 Task 19 - Calculation of the current position of the product on the belt. 113
13.1.1 Termination. 114
13.1.2 Scenario 1. 115
13.1.3 Scenario 2. 116
13.1.4 Scenario 3. 117
13.1.5 Scenario 4. 118
14 Comparison operations (comparators). 120 120
14.1 Task 22 - Comparing the value of the current speed 120
14.1.1 Termination. 120
14.1.2 Scenario 1. 120
14.1.3 Scenario 2. 121
15 Time measurement (timers). 123 123
15.1 Task 24b - Stopping the belt when the product has passed the sensor. 123
15.1.1 Termination. 123
15.1.2 Scenario 1. 124
15.1.3 Scenario 2. 125
15.1.4 Scenario 3. 126
15.1.5 Scenario 4. 127
15.2 Problem 24c - Calculating the actual belt speed. 128
15.2.1 Termination. 129
15.2.2 Scenario 1. 131
15.2.3 Scenario 2. 135
15.2.4 Scenario 3. 139
15.2.5 Scenario 4. 142
15.3 Exercise 24d - Measuring the length of a product. 144
15.3.1 Termination. 145
15.3.2 Scenario 1. 146
15.3.3 Scenario 2. 147
15.3.4 Scenario 3. 148
15.3.5 Scenario 4. 149
You may also be interested in:
- Level:
The development environment used in the course
- Software:
Core unit family used in the course
- CPU:
A set of rules that are used to develop programme code
- Language:
Frequency converter (inverter) family used in the course
- Drive
1.529.00
- Level:
The development environment used in the course
- Software:
Core unit family used in the course
- CPU:
A set of rules that are used to develop programme code
- Language:
Frequency converter (inverter) family used in the course
- Drive
489.00 Original price was: 489.00 zł.49.00 Current price is: 49.00 zł.
- Level:
The development environment used in the course
- Software:
Core unit family used in the course
- CPU:
A set of rules that are used to develop programme code
- Language:
Frequency converter (inverter) family used in the course
- Drive
1.579.00
- Level:
The development environment used in the course
- Software:
Core unit family used in the course
- CPU:
A set of rules that are used to develop programme code
- Language:
Frequency converter (inverter) family used in the course
- Drive
489.00 PLN Original price was: 489.00 zł.49.00 PLNCurrent price is: 49.00 zł.
- Level:
The development environment used in the course
- Software:
Core unit family used in the course
- CPU:
A set of rules that are used to develop programme code
- Language:
Frequency converter (inverter) family used in the course
- Drive
1.529.00 PLN
- Level:
The development environment used in the course
- Software:
Core unit family used in the course
- CPU:
A set of rules that are used to develop programme code
- Language:
Frequency converter (inverter) family used in the course
- Drive
489.00 PLN Original price was: 489.00 zł.49.00 PLNCurrent price is: 49.00 zł.
- Level:
The development environment used in the course
- Software:
Core unit family used in the course
- CPU:
A set of rules that are used to develop programme code
- Language:
Frequency converter (inverter) family used in the course
- Drive
1.579.00 PLN
- Level:
The development environment used in the course
- Software:
Core unit family used in the course
- CPU:
A set of rules that are used to develop programme code
- Language:
Frequency converter (inverter) family used in the course
- Drive
489.00 Original price was: 489.00 zł.49.00 Current price is: 49.00 zł.
- Level:
The development environment used in the course
- Software:
Core unit family used in the course
- CPU:
A set of rules that are used to develop programme code
- Language:
Frequency converter (inverter) family used in the course
- Drive
1.529.00
- Level:
The development environment used in the course
- Software:
Core unit family used in the course
- CPU:
A set of rules that are used to develop programme code
- Language:
Frequency converter (inverter) family used in the course
- Drive
489.00 Original price was: 489.00 zł.49.00 Current price is: 49.00 zł.
- Level:
The development environment used in the course
- Software:
Core unit family used in the course
- CPU:
A set of rules that are used to develop programme code
- Language:
Frequency converter (inverter) family used in the course
- Drive
1.579.00
- 1
- 2